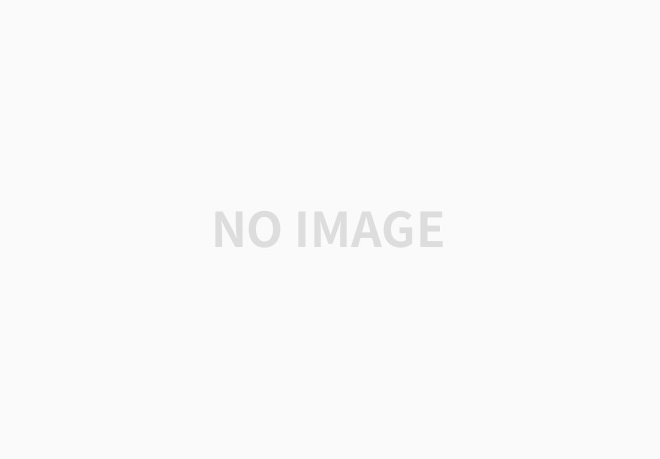
우리는 반도체 전쟁에 대한 News 접하여 살아가고있다.
최근에는 멍멍이도 반도체. AI 공부를 하고 있다고 하니, 인간으로서 개 보다 못할 순 없다.
이러한 반도체 열기는 시작에 불가하며, 개나 돼지들도 반도체 공부를 하지 않으면 먹고살기 힘든 세상이 오리라 생각한다.
최근 들어 파워 반도체. 하이 브리드 반도체 사장이 매우 빠르게 변화되고 있다. 한국에서는 오직 삼성반도체 쳐다보면서 살고 있는 동안 중국은 다양한 분야에 파워 반도체 생산 및 제조기술력 향상을 하고 있다. 특히 이러한 분야는 전기차 업종 BYD. CRRC. DongGfeng Motor. GAC Group. 및 중국의 반도체 기업들이 Power Chip 생산에 매우 높은 기술 및 생산성 높은 제품을 생산하고 있다.
반도체는 Ram Memory Module 있는 것이 아니다. 전기차 분야에 Custom 하이브리드 IC 적용이 너무 많기 때문이다. 이러한 기업에 350L 장비가 사용하고 있는 것에 대하여 장비 소개를 하고자 한다.
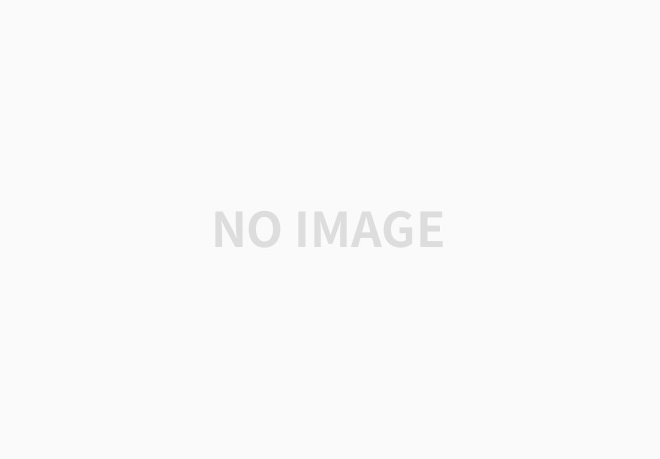
Power IC 생산에 있어 최적화된 장비이다.
네덜란드의 ASML 장비보다 Application 이 높다고 개발자는 자동 한다.
이것은 가격 대비 성능을 의미하기도 한다.
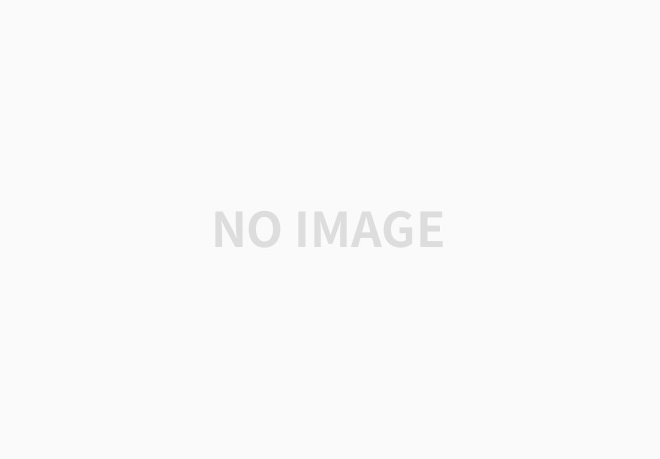
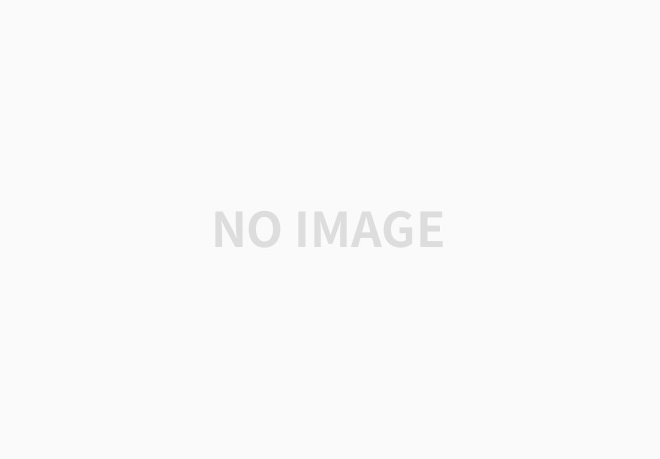
Power Die Bonder (top View)
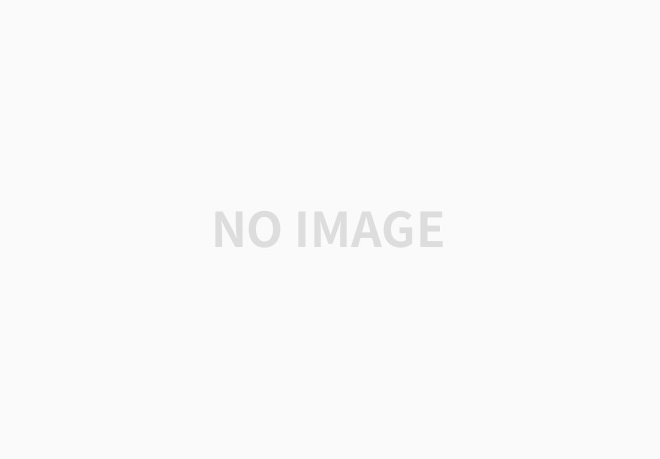
▶ Auto wafer Pick & Place
▶ Bond Dispenser
▶ Tape Feeder Platform
▶ Auto Tray Cassette 사용
▶ Auto Nozzle Change Sys
▶ IGBT(DBC) Module Carrier.
▶ Wafer Cassette
▶ Tray Cassette
다양한 소재 작업을 하나의 장비에서 작업 실현 가능한 장비 입니다
350L Die Chip Assembly

AUTOTRONIK의 최신 IGBT Power Diebonder는 다음 시트에 소개됩니다. 장점은 이러한 여러 유형 및 재료 사양이 동시에 하나의 고정밀 마운팅 장비와 호환된다는 것입니다.
작업 공정 흐름도 of IGBT Module

IGMT Assemby
A. Primary Processes 기본

Process Flow : Solder Paste screen printed to DBC (ceramic) -> Chips/Dies placing by SMT Pick & Place machine -> Soldering (Vacuum Reflow Oven)
Advantage : Use of normal PCBA processing with existing SMT equipment, to save the expensive investment cost of new production line.
Dis-advantage :
1. 진공 리플로우 솔더링 처리는 솔더 페이스트에서 기포를 최대 90%까지만 제거하고 냉각 효과를 줄이며 결함 제품이 증가합니다.
2. 솔더 페이스트가 플럭스의 가스화 폭발로 오염을 일으키는 주변 칩/다이의 표면에 튀길 수 있습니다.
3. 냉각된 땜납 층에 기포가 많아 패드 산화, 저항 증가 및 땜납 층 균열 가능성이 높아집니다.
4. 기포는 또한 DBC 모듈의 방열을 차단하여 IGBT 전원 모듈의 갑작스러운 고장 또는 손상을 초래합니다.
5. 스크린 인쇄 공정으로 IGBT 공정에서 이중 칩 오버레이 패치(다중 배치)의 공정 요구 사항을 충족할 수 없습니다.
6. 제품 불량률이 높아 극도로 높은 온도와 높은 진동에서 작업 요구 사항을 견딜 수 없습니다.
7. 웨이퍼 다이는 원래 SMT 칩 마운터에 직접 로드할 수 없으며 트레이 캐리어 로드 또는 테이프 형식 로드로 변환해야 합니다.
8. 스크린 프린터 및 SMT 칩 마운터는 이러한 컨베이어에 무거운 IGBT 캐리어 로딩 및 이송이 허용되지 않습니다.
B. Advanced Processes

Process Flow :
DBC boards carrier loading to SV350L -> Solder-plate placing -> Chips/Dies placing (Tape/ Wafer/ Tray feeder) à Soldering (Formic Acid Vacuum Reflow)
Advantage :
1. IGBT 전원 모듈 칩 실장을 위해 특별히 설계된 SV350L 장비를 사용하여 DBC 모듈의 전체 칩 어셈블리를 완성.
2. 솔더 플레이트 피더는 필요한 길이의 솔더 플레이트를 공급하고 절단한 다음 헤드를 자동으로 장착하여 DBC 보드에 배치할 수 있습니다.
3. 직접 솔더 플레이트는 플럭스로 인한 다양한 문제를 방지하고 불량품 발생을 제거할 수 있습니다.
4. 자동 웨이퍼 로딩 시스템을 갖춘 SV350L, 각 웨이퍼 카세트는 최대 25개의 플랜지와 다양한 유형의 재료 로딩을 저장할 수 있습니다.
5. 최대 가공 프로그램에 따라 다른 사양의 재료로 배치할 수 있습니다. 카세트에 25가지 유형의 웨이퍼 플랜지 재료
6. 자동 트레이 공급 시스템을 채택하여 각 트레이 카세트는 최대 구성 요소 트레이 크기에 대해 트레이 캐리어의 8개 레이어를 저장할 수 있습니다. 각각의 245*120mm;
7. 처리 프로그램에서 자동 로드 및 배치를 위해 최대 25가지 유형의 구성 요소 재료를 지원합니다.
8. 자동 웨이퍼 및 자동 트레이 시스템은 재료 카세트를 신속하게 교체하여 생산성을 향상시킬 수 있습니다.
9. SV350L 시리즈의 4 헤드 및 6 헤드 선택 가능, 다양한 부품 유형 취급이 편리하고 생산성이 향상되었습니다.
10. 포름산 진공 리플로우는 DBC 다이 솔더링 능력을 향상시키고 산화를 제거하며 공정 시간을 단축할 수 있습니다.
Dis-advantage : Higher investment cost
350 L 장비 소개

.

1. Heads : 4 / 6
2. Placement Accuracy : ±10um
3. Capacity of Placement : max.1800uph / max.2200uph (Solder-Plate + Chips Placement)
4. Size Capacity of Carrier : max. 460x350x20mm
5. Weight Capacity : max. 8kg (each carrier), (optional to 15kg)
6. Feeding System : Tape feeder (max. 3 sets of Solder-Plate feeder on Platform)
7. Tray feeder (max. 8 Tray carriers @ Tray Cassette)
8. Wafer feeder (max. 25 Wafer Flange @ Wafer Cassette)
Auto Tray System
1. Auto-Tray 시스템은 표준 기능입니다. 8개의 트레이 캐리어를 트레이 카세트에 보관할 수 있습니다. inc
2. Tray Cassette size: 264*146*H180 mm
3. Storage levels: 8 storeys
4. Capacity of Carrier: max. 245*120*10mm (Thickness of component + tray)
5. Compatibility: 최대 8종의 Tray Component 본딩 프로그램.
(하나의 재료 유형만 설정할 수 있습니다. 각 트레이 캐리어)



component Tray
Auto Wafer System
Std. with 6”/8” or 8”/12” wafer platform selectable
Std. with one wafer cassette (choose one within 6”/ 8” /12” wafer cassette)

Compatibility : max. 25 types of Wafer Die for a bonding program

Waffer Feeding platforms


Bonder Head Module
1. 각 헤드의 Z축과 R축은
2. 독립 서보 모터. X/Y축 해상도는 0.002mm
3. R축 분해능은 ±0.02°(360º 회전)
4. Z축의 이동 높이는 최대입니다. 35mm,
5. Z축 분해능은 ±0.005mm입니다.

Automation System

Dispensing Control

1. Power Required
|
AC 220V (±10% ), 50Hz, 0.25kw
|
2. Power Switch
|
With an independent power switch
|
3. Compress-air Required
|
80psi (5.5bar)
|
4. Compress-air Adjustment
|
Tunning switch x 1 , accuracy :±0.1psi
|
5. Air input to Valve of Syringe
|
Quick coupling x 1
|
6. Low-pressure Alarm
|
Individual alarm with margin adjustable
|
7. Pressure Output Monitoring
|
LCD pressure meter x 1
|
8. Work Frequency Counter
|
LED Counter x 1
|
9. Air-source Pressure Monitoring
|
LCD Display x 1
|
Operation System

Autotronik Interactive software built on the Win 10 OS system platform,
English / Chinese online switchable and other language selectable (option).
The real-time production situation has show on the Intuitive Screen.
±10um placement accuracy was improved by precise positioning system.
Feeding platforms editing menu is Simple and Clearly,
supported max. 25 component types of each feeding platform of Tray and Wafer.
Online software upgrade and remote technical guidance.
Software Parameter

사용자 모니터링을 위해 실시간 작동 칩 배치 상태가 화면 상단에 표시되었습니다.
Features of Glue Dispensing
|
Features of Die Bonding (Placement)
|
다양한 광원 선택 가능
(백색/청색/적색/적외선/축방향). |
남은 칩과 감지된 NG 칩은 화면 하단의 재료 보드에 표시됩니다.
|
편리한 부표형 광원 조건 조정.
|
사용자 모니터링을 위해 실시간 작동 칩 배치 상태가 화면 상단에 표시되었습니다.
|
Dispensing route is multi segment combination, user can add / delete / movable and traceable the route, with optional function for the glue route breaking detection (min. 0.3mm break defect)
|
The identification accuracy of materials can be set independently, and compared with the PR template for score result, the low score will be classified as NG.
|
Flexible and interactive application window to make user friendly.
|
The figure comparation score of material had shown on right side convenient for monitoring.
|
Able to monitoring the glue dispensing condition at small window on right.
|
Screen showing the production data as: productivity, average UPH, % of good, % of NG…etc.
|
Paramter Table
350L-4P

350L-6P

Optional Parts

Wafer Cassette

Ejection Pin Set

Nozzle

Gel Dispenser Sys
별도 자료 요청은 info@namaSMT.com 하여 주세요



Korea Distributor NamA Seoul Korea
장비 사진 :













관련 자료

Die Bonder

Effective Area

Laser 높이 측정

Die Chip 실장

Bulk 부품 실장

Feeding Platform Multi-type of Feeding Platform




고성능 Vision Camera Sys

Pressure
Bonding force (standard range) : 30g-500g (optional up to 2000g)

Tray Feeding
트레이 공급 플랫폼: 16개 허용. 2”의 Gel-Pak / JEDEC 재료 트레이를 각 트레이 공급 그룹에 배치하고 최대 3개의 그룹이 기계에 설치 가능합니다.



Lab N2 reflow
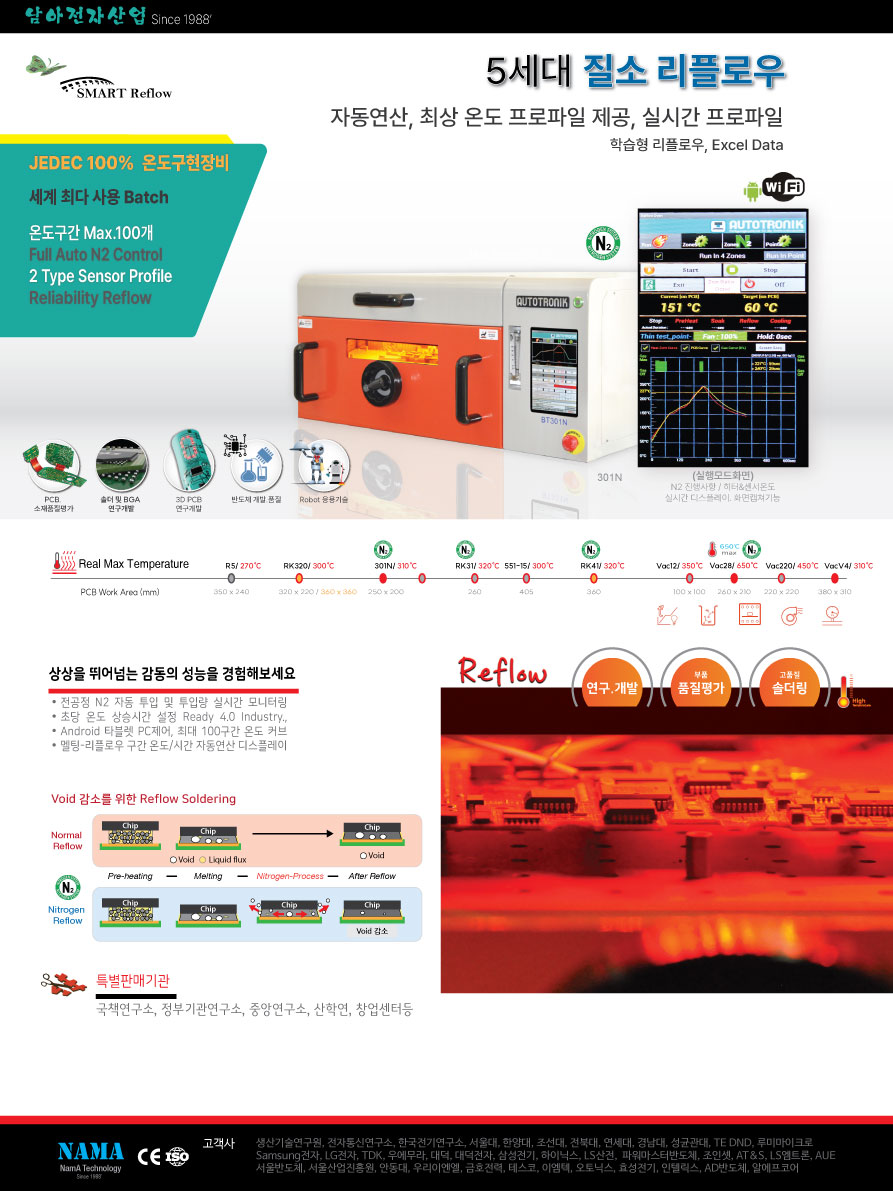

'18. 기술 정보 모음. > L. 기술정보' 카테고리의 다른 글
SMD Reel 2mm Pitch counting Adapter (0) | 2024.09.04 |
---|---|
Small Reflow 네비케이션 방식의 PC 제어 Smart Reflow (0) | 2017.11.07 |
Laser Thickness Gauge 동영상 (0) | 2017.02.23 |
Laser Thickness Gauge (1) | 2017.02.23 |
4세대 SMD Assembly 장비들 . (0) | 2016.10.22 |