
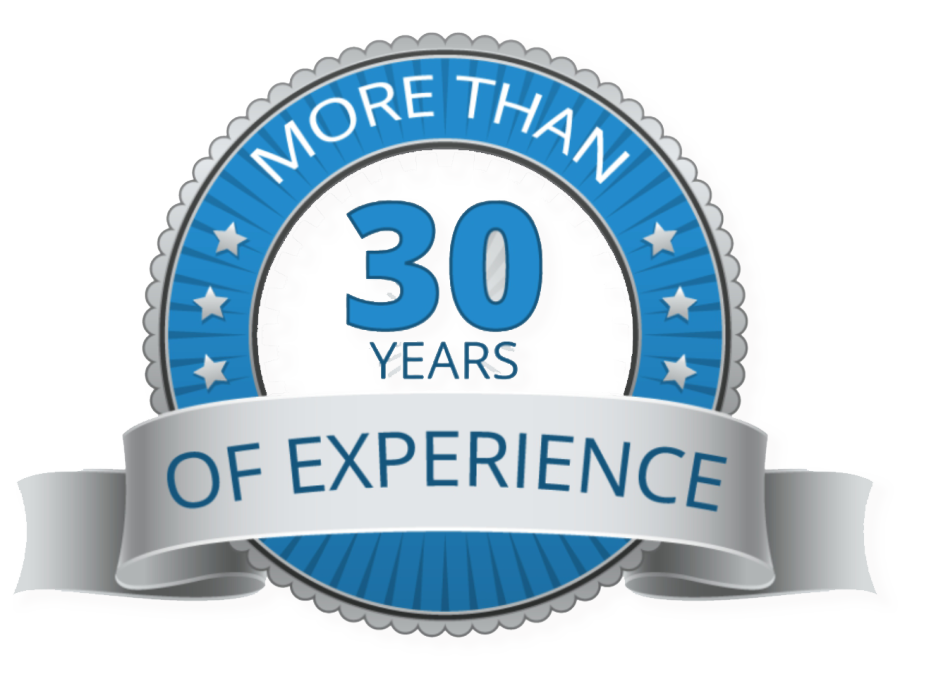

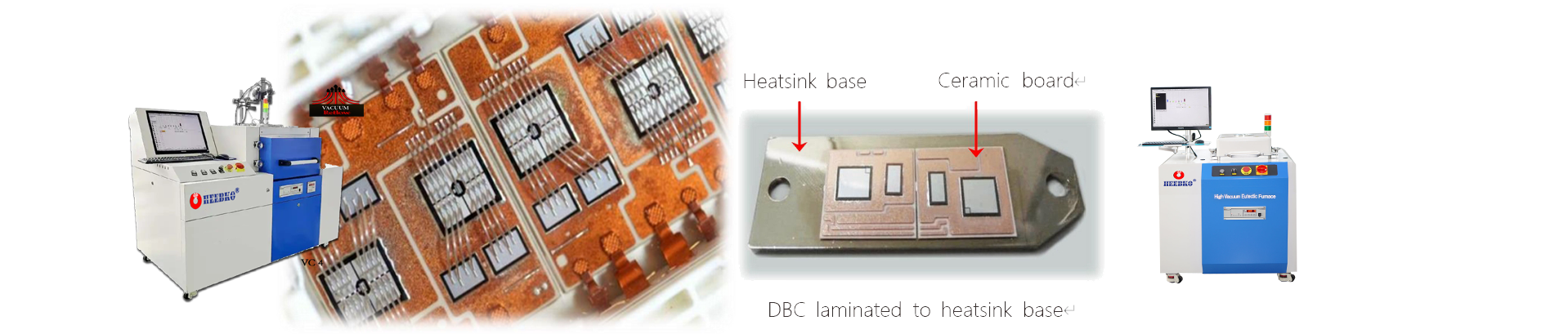
IGBT 전력 소자 진공 납땜 시스템은 진공 환경에서 IGBT 전력 소자를 납땜하기 위한 특수 장비입니다. 산화를 방지하고 고품질 납땜 접합을 보장하는 것 외에도 이 시스템은 납땜 중에 무산소 분위기를 조성합니다. 진공 납땜, 납땜을 통해 장치의 신뢰성과 성능을 향상시킬 수 있습니다. 이는 전력 전자 장치, 모터 드라이브 및 재생 에너지 시스템과 같은 민감한 전자 응용 분야에 적합합니다. 정밀한 납땜을 보장하는 것 외에도 견고하고 효율적인 전자 부품에 대한 위험 결함 위험을 최소화합니다.
IGBT Assemby
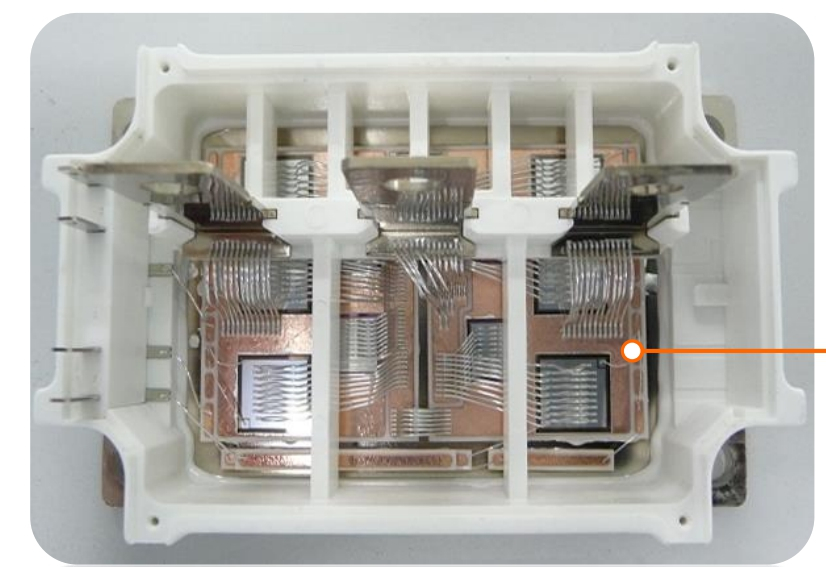
남아전자산업의IGBT Power Diebonder 장비를 아래에 소개합니다. 재료의 종류와 사양이 동시에 하나의 고정밀 실장 장비와 호환된다는 장점이 있습니다.
https://www.namasmt.com/products/product_detail.html?idx=331&cat01=02&cat02=

IGBT Assemby Work Lay out
IGBT 생산 작업 공정표 " 남아전자산업에서는 IGBT 실장 + Vacuum Reflow + Curing 장비 공급 가능 합니다.
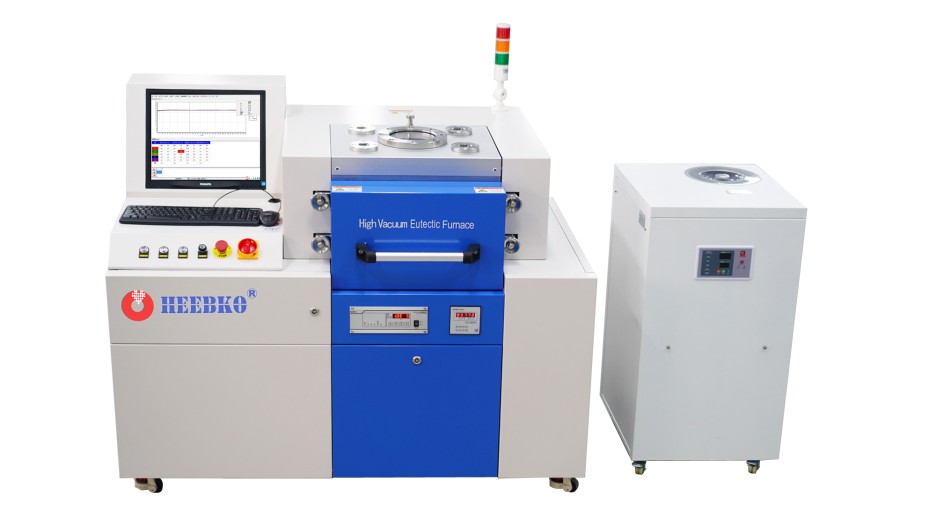
IGBT 전력 장치에 진공 납땜 시스템을 사용하면 어떤 이점이 있습니까?
IGBT 전력 장치에 진공 납땜 시스템을 사용하면 다음과 같은 몇 가지 중요한 이점을 얻을 수 있습니다.
1. 산화 방지
IGBT 전력 장치는 산소를 제거하는 진공 환경을 통해 고품질 솔더 조인트와 장기적인 신뢰성을 보장하도록 설계되었습니다.
2. 상된 솔더 품질
솔더 품질이 더욱 일관되어 IGBT와 PCB 간의 연결이 더욱 강력하고 일관되게 이루어집니다.
3. 보이드 형성 감소
진공 납땜은 솔더 조인트의 Void 형성을 줄이는 데 도움이 됩니다. 이는 열 및 전기 전도성을 유지하는 데 중요하며 IGBT 전력 장치의 전반적인 성능을 향상시킵니다.
4. 향상된 Electrica Peelectrical 성능
보이드가 줄어들고 솔더 품질이 향상되면 IGB 장치 전력 손실이 발생하고 효율성이 향상됩니다.
5. 밀폐형 밀봉
진공 납땜은 IGBT 전력 장치의 밀폐형 밀봉을 달성하여 습기나 오염 물질의 유입을 방지할 수 있으며 이는 특히 열악한 환경의 응용 분야에 중요합니다.
6. 민감한 부품의 납땜
IGBT는 고온 및 대기 조건에 민감하므로 진공 납땜을 사용하면 납땜 공정을 정밀하게 제어할 수 있어 위험 장치의 손상 위험을 줄일 수 있습니다.
7. 일관성 및 재현성
진공 납땜 공정은 생산 배치의 여러 IGBT 전력 장치에 걸쳐 균일한 납땜 접합을 보장하여 일관되고 재현 가능한 결과를 보장합니다.
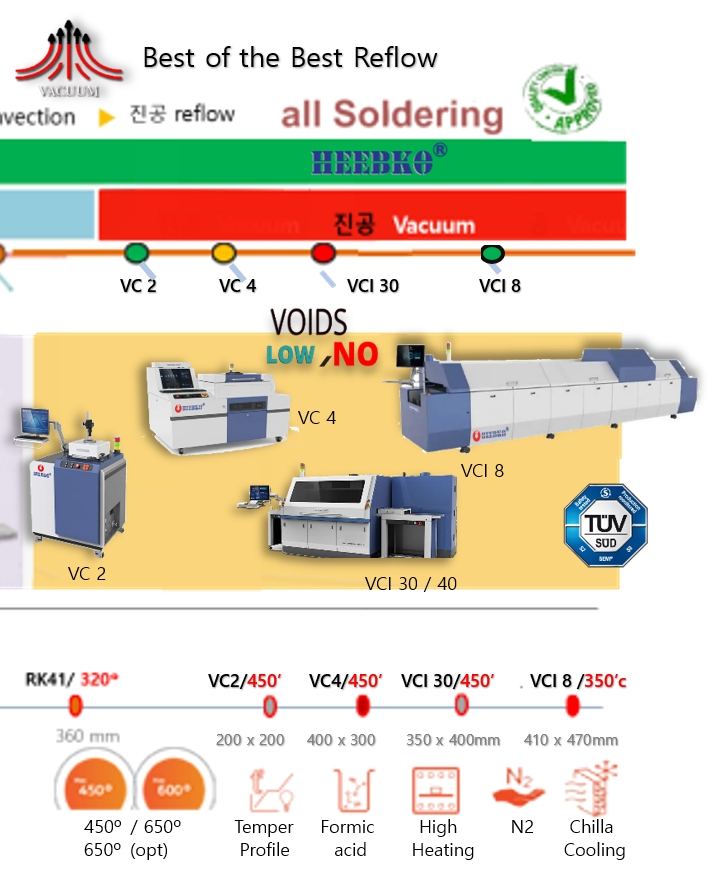
Primary Processes

.

Void 감소를 위한 진공 리플로우 VCi 40 Model
DBC 보드 캐리어 로딩 솔더 플레이트 배치 칩/다이 배치(테이프/웨이퍼/트레이 피더) 솔더링(포름산 진공 리플로우)
IGBT 전원 모듈 칩 장착용으로 특별히 설계된 SV350L 장비를 사용하여 DBC 모듈의 전체 칩 어셈블리를 완성합니다.
1. SV350L은 SMT 테이프 피더, 트레이 피더 및 웨이퍼 플랜지 피더와 호환되어 로딩 및 언 로딩이 가능합니다.
2. 솔더 플레이트 피더는 필요한 길이의 솔더 플레이트를 공급하고 절단한 다음 헤드를 자동으로 장착하여 DBC 보드에 배치할 수 있습니다.
3. 솔더 플레이트를 직접 배치하면 플럭스로 인한 다양한 문제를 방지하고 불량 제품의 발생을 없앨 수 있습니다.
4. 자동 웨이퍼 로딩 시스템이 장착된 SV350L은 각 웨이퍼 카세트에 최대 25개의 플랜지와 다양한 유형의 재료 로딩을 저장할 수 있습니다.
5. 가공 프로그램에 따라 재질의 사양을 최대로 배치할 수 있습니다. 카세트에 포함된 25가지 유형의 웨이퍼 플랜지 재료
6. 자동 트레이 공급 시스템을 채택한 각 트레이 카세트는 최대 구성 요소 트레이 크기에 대해 8겹의 트레이 캐리어를 저장할 수 있습니다. 각각 245*120mm;
7. 처리 프로그램에서 자동 로딩 및 배치를 위해 최대 25가지 유형의 구성 요소 재료를 지원합니다.
8. 자동 웨이퍼 및 자동 트레이 시스템은 재료 카세트를 신속하게 교체하여 생산성을 향상시킬 수 있습니다.
9. SV350L 시리즈는 4개 헤드와 6개 헤드를 선택할 수 있으며, 다양한 부품 유형을 취급하기 편리하고 생산성이 향상되었습니다.
10. 포름산 진공 리플로우는 DBC 다이 납땜 능력을 향상시키고 산화를 제거하며 공정 시간을 단축할 수 있습니다.
IGBT 실장 장비 Introduction
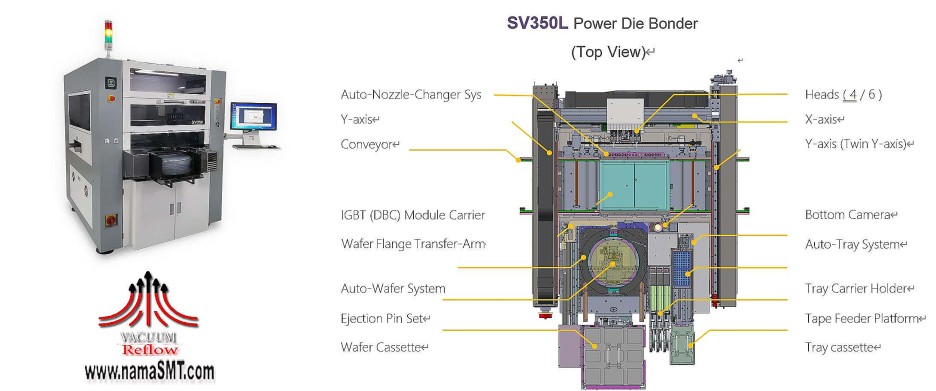
1. Heads : 4 / 6
2. Placement Accuracy : ±20um
3. Capacity of Placement : max.1600uph / max.2200uph
( Solder-Plate + Chips Placement )
4. Size Capacity of Carrier : max. 420x350x20mm Weight Capacity
5. Weight : max. 8kg (each carrier)
6. Feeding System : Tape feeder (max. 3 sets of Solder-Plate feeder on Platform)
Tray feeder (max. 8 Tray carriers @ Tray Cassette) Wafer
feeder (max. 25 Wafer Flange @ Wafer Cassette) 6”/ 8”/ 12”
Wafer Cassette is selectable
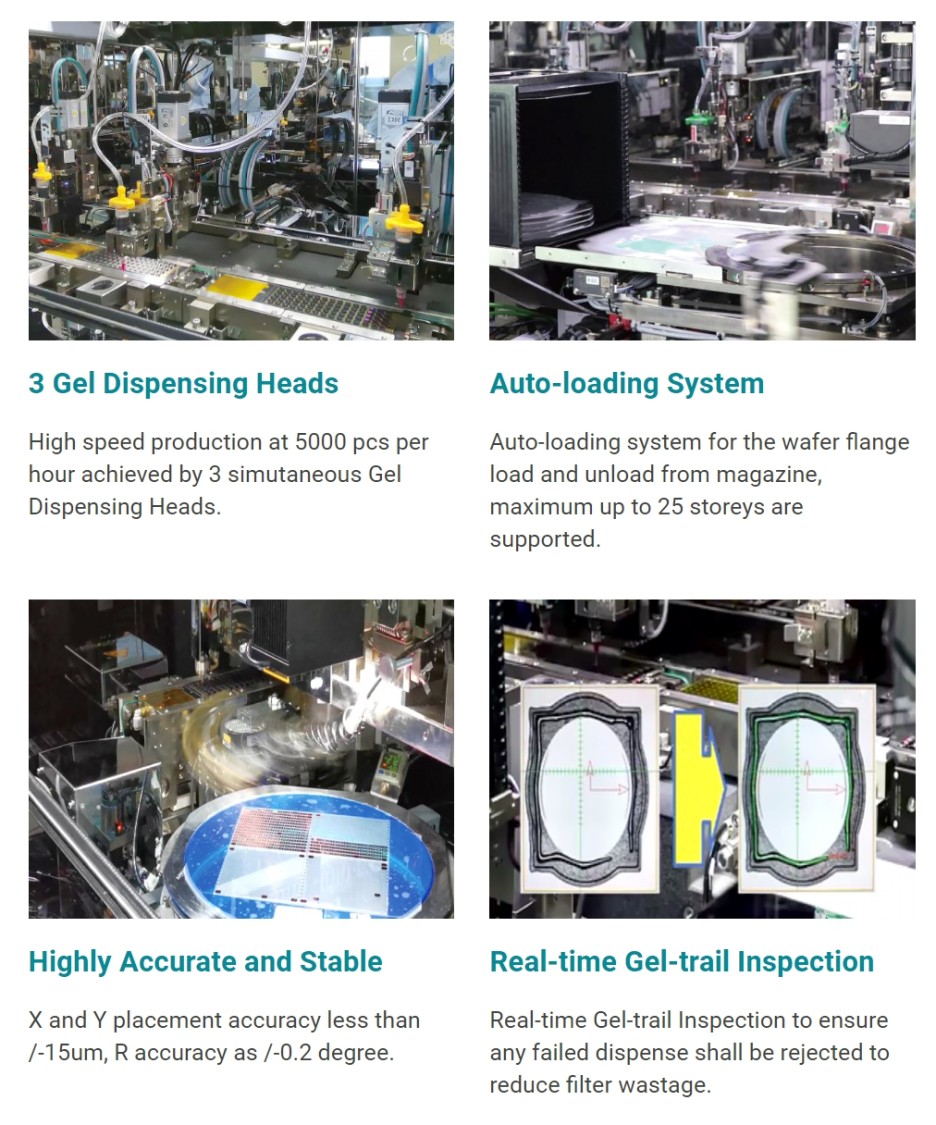
여러유형의 packaging 사용 가능
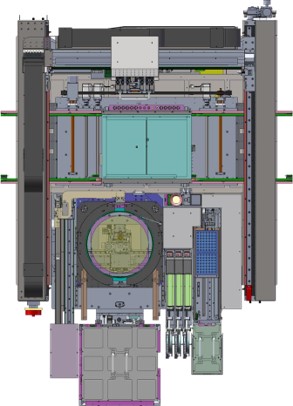
Tape Feeder Platform
Feeder Platform has 8 slots for 8mm Std. SMT Tape Feeder, or up to 3 Solder-plate Tape Feeder can be installed.
Available the types of Solder-plate Tape Feeder (option) as
HT2-14 / HT12-16 / HT22-36
and the corresponding solder-plate feeding size is 2*2~14*14mm / 12*12~26*26mm / 22*22~36*36mm Solder-plate is auto-cut on the feeder and
length adjustable in range of feeder specification
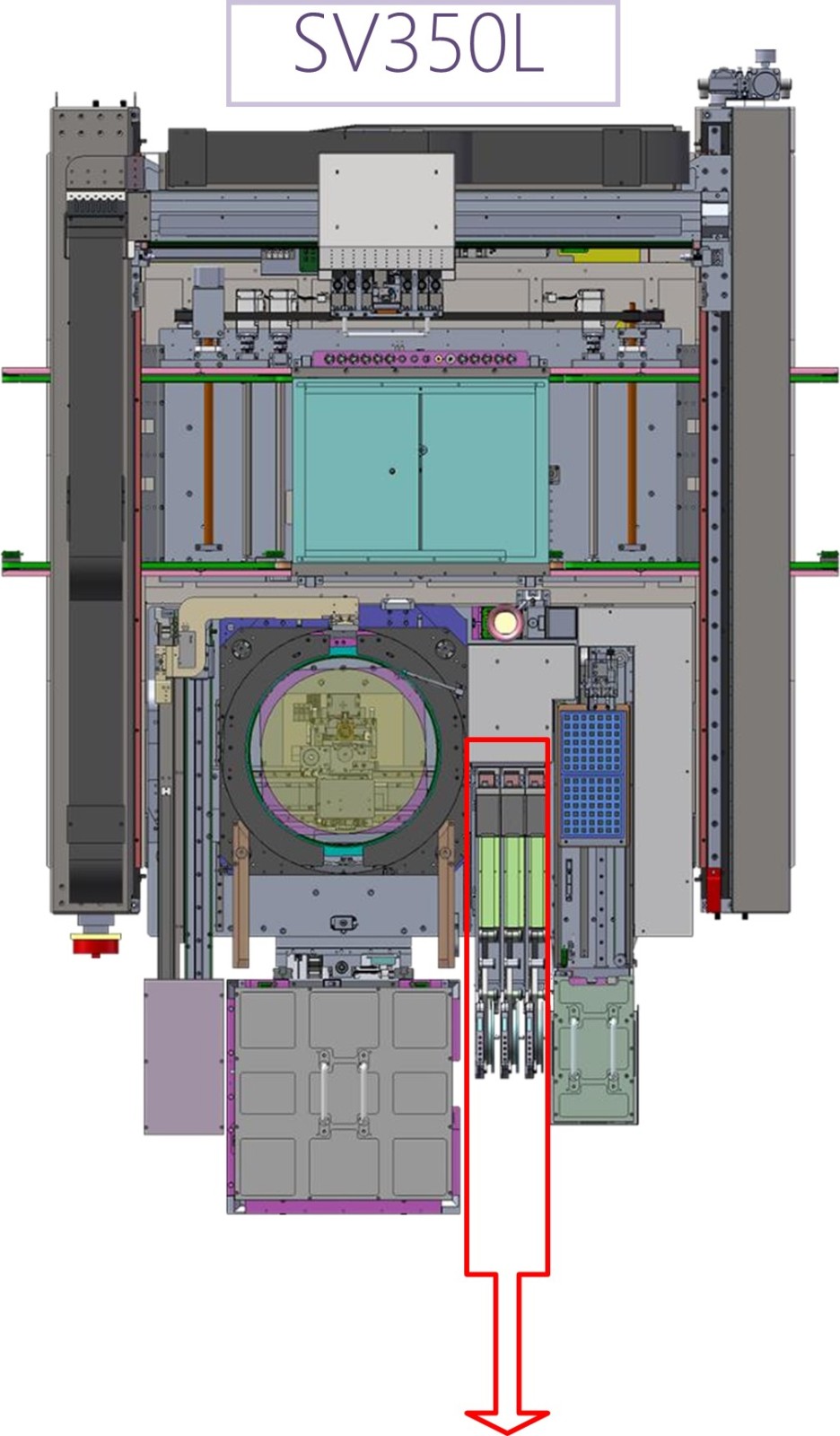
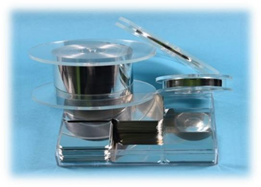
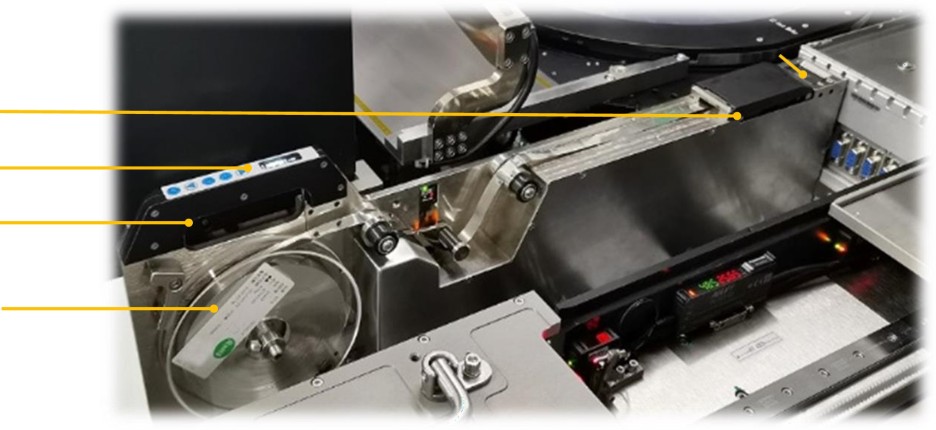
Discharge Port Auto-cutter
Keypad + LED screen
Feeder Handle
Tape reel form Solder-plate
Auto-Tray System
The Auto-Tray System is a standard feature
8 Tray Carriers can be stored in the Tray Cassette (included) Tray Cassette size: 264*146*H180 mm
Storage levels: 8 storeys
Capacity of Carrier: max. 245*120*10mm (Thickness of component + tray)
Compatibility: max. 25 types of Tray Component for a bonding program (only one material type can be set for each tray carrier)
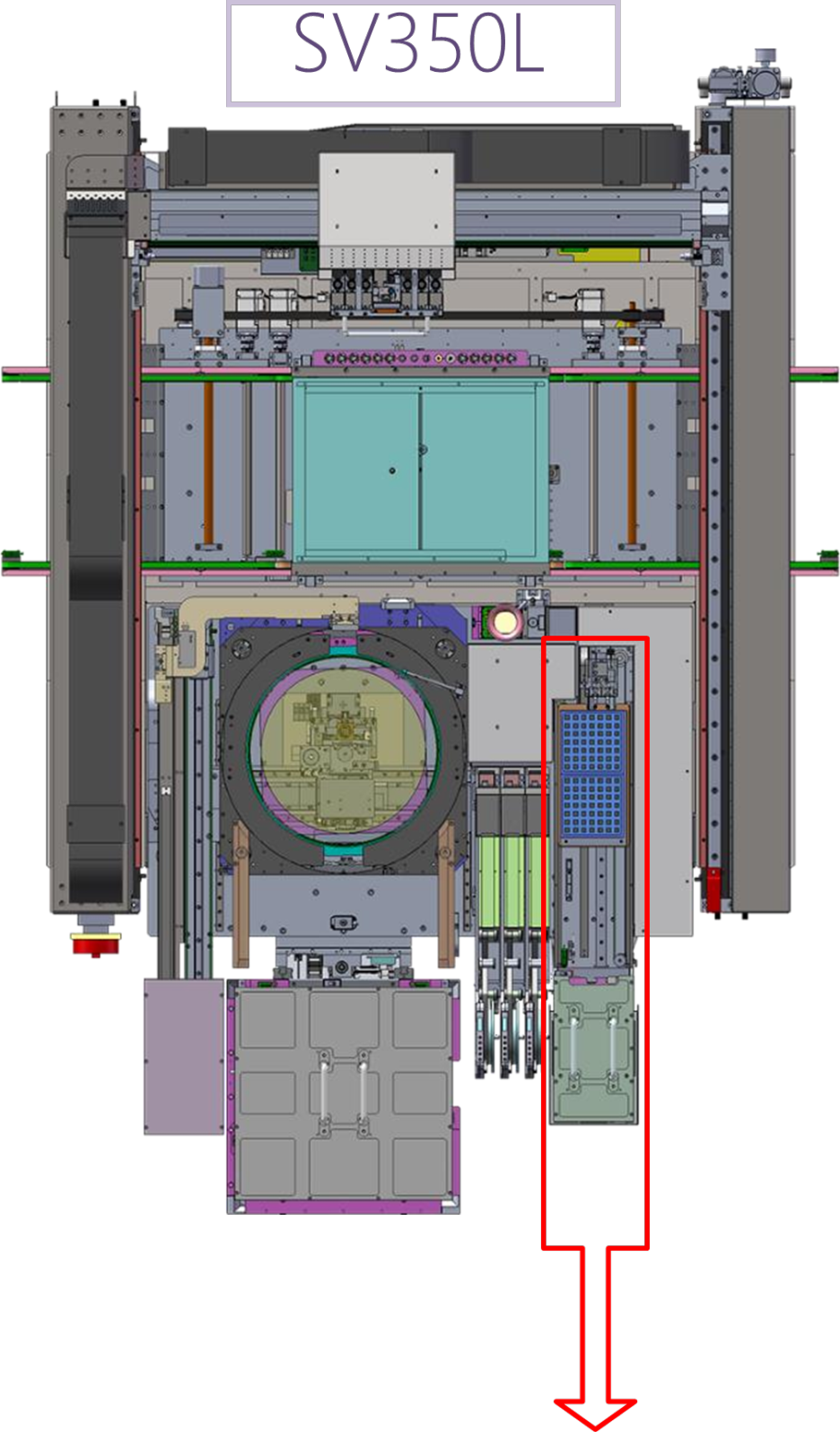
The Auto-Tray System is a standard feature
8 Tray Carriers can be stored in the Tray Cassette (included) Tray Cassette size: 264*146*H180 mm
Storage levels: 8 storeys
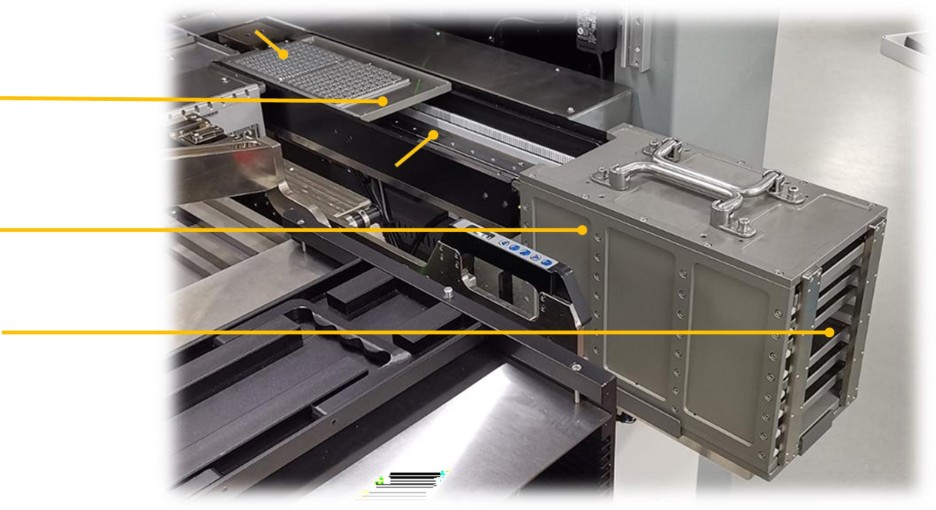
Component Tray Tray
Carrier Holder
Truck Rail
Tray Cassette max. 8 Tray Carrier store
Auto-Wafer System
Std. with 6”/8” wafer platform ( 8”/12” wafer platform is option)
Std. with one wafer cassette (choose one within 6”/ 8” /12” wafer cassette)
Wafer Cassette
|
6” (inch)
|
8” (inch)
|
12” (inch)
|
Size (mm):
|
222*212*H143
|
288*276*H205
|
388*394*H193
|
Storage:
|
25 flanges
|
25 flange
|
13 flanges
|
Flange Diam.:
|
227 ±1mm
|
295 ±1mm
|
399 ±1mm
|
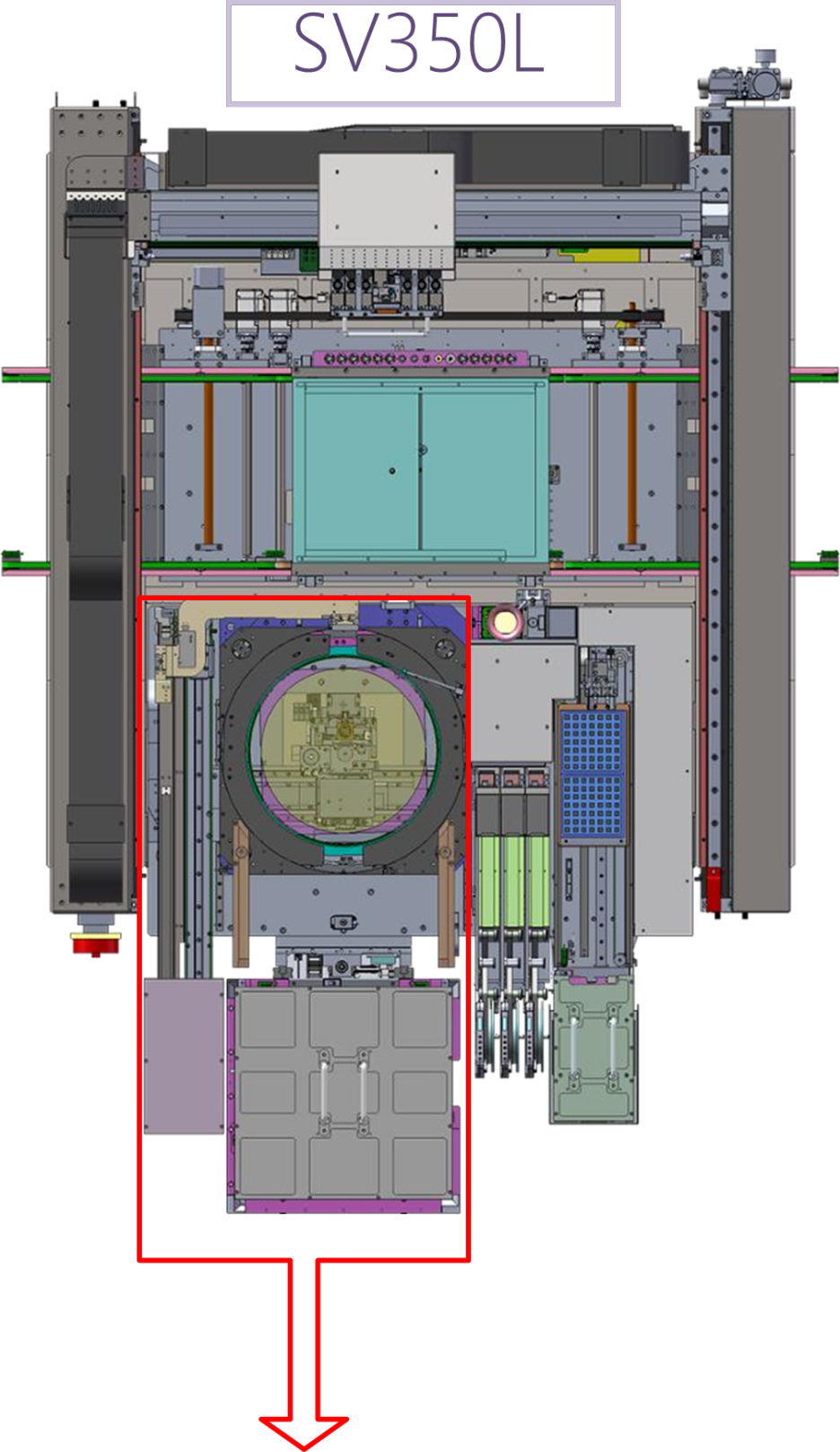
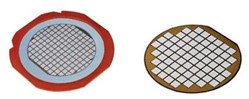
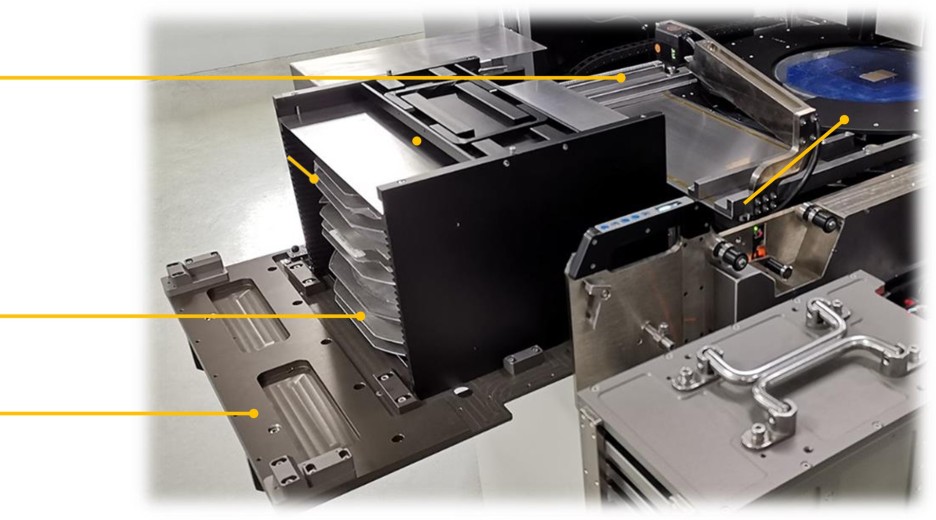
Truck Rail
Wafer Cassette
Wafer Flange Holder (Loading Zone)
(switchable two sets of diaphragm ring and tracks)
max.25 /13 wafer flange in a cassette Large platform for 8"/ 12" wafer Cassette
Small platform for 6"/ 8" wafer Cassette
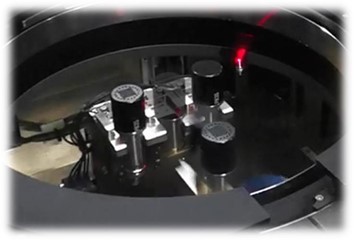
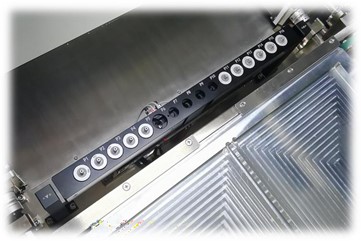
Fit for various spec. of Wafer Dies placement, 3 Eject-Pin auto exchanging programmable, fastest exchange just 4 sec only
|
Up to 16 Nozzles can be stored for exchange, for wider application of different materials spec., and auto-changing by system programmable
|

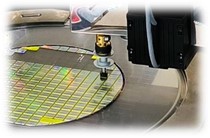
Optional Dispensing System for SV-series, it can provide the One-Shop solution of Gel or Solder dispensing requirement
|
Up to 16 Nozzles can be stored for exchange, for wider application of different materials spec., and auto-changing by system programmable
|

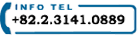
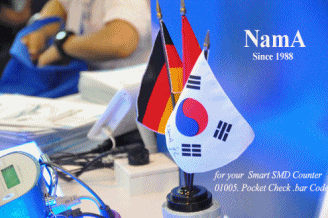
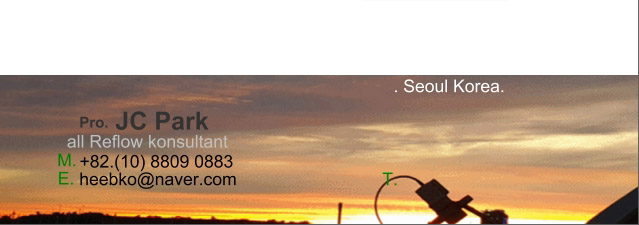
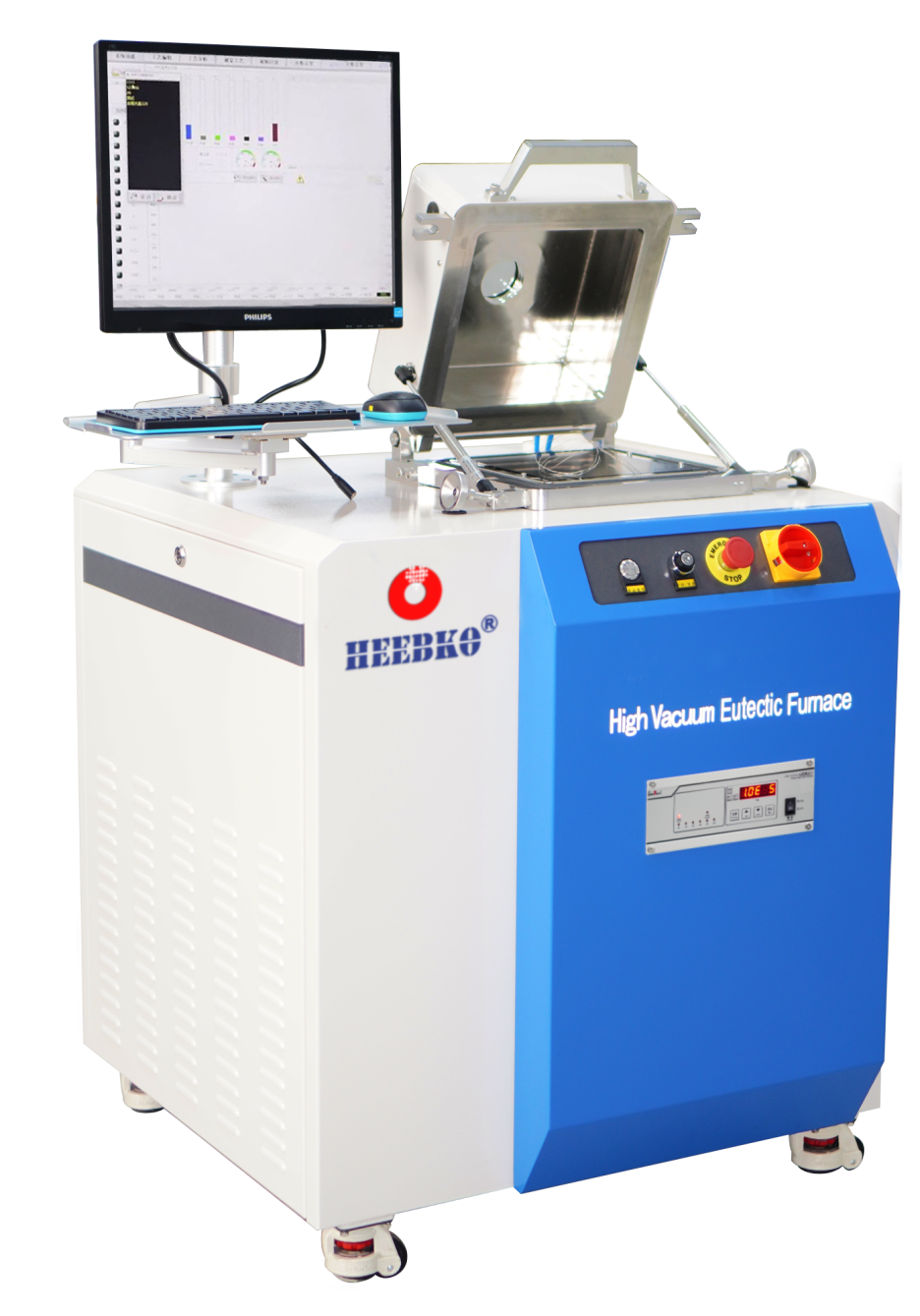
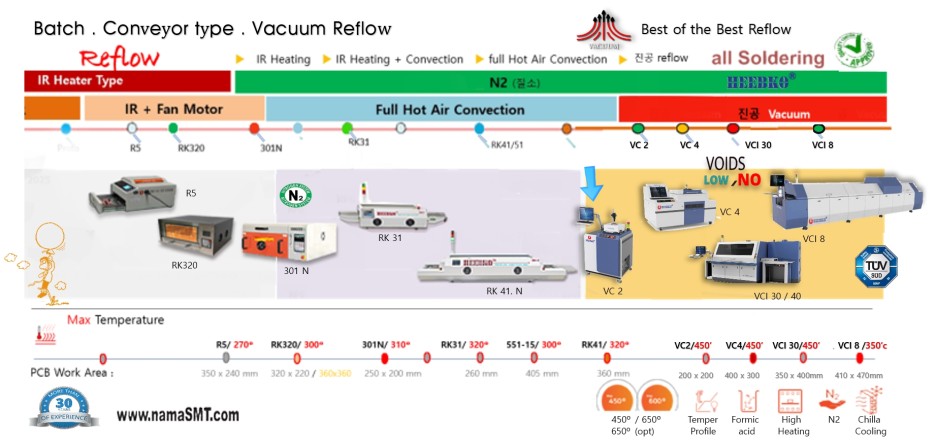
'4. Vaccum Reflow > 진공 Reflow' 카테고리의 다른 글
진공리플로우 VC Series reflow (0) | 2024.03.07 |
---|---|
진공리플로우 AD (0) | 2024.02.29 |
Vacuum Reflow for Lab. Prototype . 기능 비교표 (0) | 2024.02.09 |
Vapor Soldering (증기방식) 정밀 온도를 위한 Reflow 동영상 (0) | 2013.06.20 |
Vacuum [진공] Reflow Machine (0) | 2009.05.13 |